Metal 3D Printing
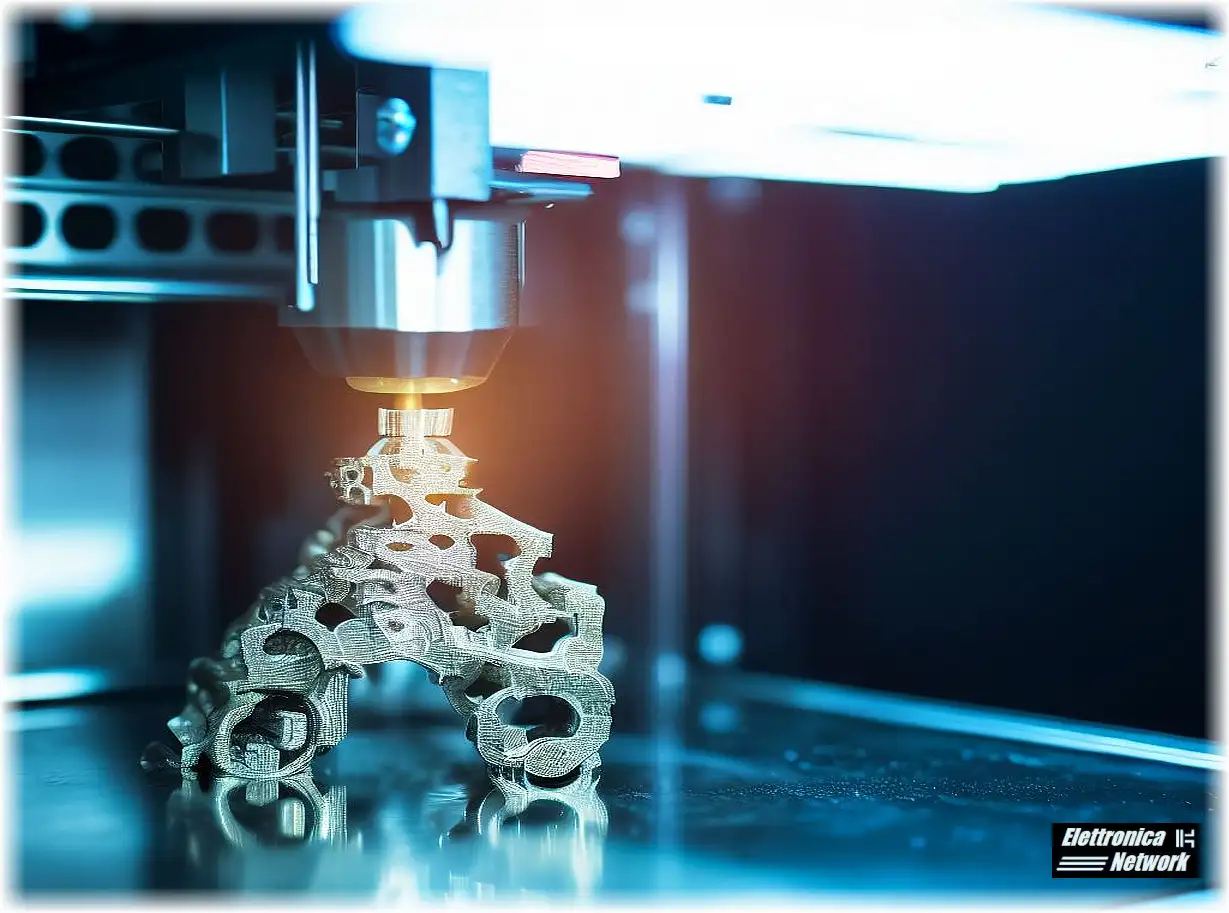
How Metal 3D Printing Works?
Metal 3D printing is an advanced technology that allows you to create three-dimensional metal objects with great precision and detail. This technology uses different 3D printing techniques, including metal deposition printing (DM) and selective laser sintering (SLS). 3D metal printing is used in many industry sectors, such as the aerospace industry, the medical industry and the automotive industry.
Thanks to its ability to create metal objects with great precision and detail, The 3D metal printing allows you to produce personalized parts and components with complex geometries and smooth surfaces, that would be difficult or impossible to achieve with traditional production methods.
Generally, The 3D metal printing is an advanced technology that is revolutionizing the approach to the production of metal parts and components, allowing to create objects with greater precision and detail and further improving the efficiency and sustainability of industrial production.
3D metal printing techniques
Among the most popular technologies for 3D metal printing, There is metal deposition printing (DM), This provides for the merger of metal powders through a thin laser ray, which creates a solid layer for layer. The metal powder is distributed on a substrate and the laser beam melts the dust particles, creating the desired object. The DM process allows you to create objects in a wide range of metals, including steel, titanium and aluminum.
Another technique is selective laser sinterization (SLS) which consists in the merger of metal powders through a laser beam, which creates a solid layer for layer. However, Unlike the DM, The SLS process does not require the use of a substrate, since metal powder is merged directly into a solid object. The SLS process allows you to create objects in a wide range of metals, including steel, titanium and nickel.
There is also further technology still in development, based on the extrusion of special filaments for 3D metal printing, which are made using a combination of plastic polymers mixed in an appropriate way with metal steel powders, titanium, aluminum, copper and nickel. and others.
Once printed, 3D metal objects can be left to exposure to an activating agent, such as heat, which causes the fusion of metal particles and the complete evaporation of plastic polymers without changing the shape of the object. In this way, 3D metal objects can be designed to adapt to different environmental conditions or to perform specific tasks.
However, The 3D FDM printing of the metal has some technical challenges, including the difficulty of melting and depositing filaments containing metal dust with a good adhesion between the various layers.
In addition, The 3D FDM printing of the metal requires very high printing temperatures, which can be difficult to control and can cause deformations or distortions of the object.
Despite the technical challenges, The 3D FDM printing of the metal has the potential to revolutionize the approach to the production of metal parts and components, allowing to create objects with greater flexibility and functionality.
However, at the moment, The 3D FDM printing of the metal is still a technology in the development phase and is not yet widespread in industry.
What can be printed with 3D metal printing?
The 3D metal printing is used in the aerospace industry for the production of light and resistant aircraft parts, In the automotive industry for the production of personalized spare parts for vehicles and in the medical industry for the production of personalized prostheses and anatomical models for surgical planning.
Generally, The 3D metal printing allows you to produce complex parts that would be difficult or impossible to create with traditional production methods. For example, The 3D printing of the metal allows you to create parts with complex geometries and even with smooth surfaces, which can be used in many different applications.
In addition, The 3D metal printing allows you to create personalized and unique items, that meet the specific needs of the customer. Thanks to its flexibility and the ability to create parts with greater precision and detail, The 3D printing of the metal is revolutionizing the approach to the production of metal parts and components, helping to further improve the efficiency and sustainability of industrial production.
The 3D metal printing is low -cost?
The 3D metal printing can be expensive compared to traditional 3D printing, But there are some technical details and materials that can help reduce costs. For example, The 3D printing of the metal using metal deposition technology (DM) or selective laser sinterization (SLS) It can be more expensive than the 3D FDM printing (Fused Deposition Modeling).
However, There are some hybrid techniques that can reduce the costs of 3D metal printing. For example 3D FDM Metal printing, which builds the three -dimensional object by extruding a special filament consisting of metal powders mixed with plastic polymers, It is decidedly cheaper than metal deposition technology (DM) and selective laser sinterization (SLS).
However, the cost of the same filaments and the necessary post -process process should not be overlooked, which consists in the thermal merger of the metal powders still present among the plastic polymers that give shape to the 3D object which can thus take on a full metal consistency.
The optimization of printing parameters can also reduce production costs. In addition, The use of low -cost 3D printers or sharing machines between multiple users can further reduce costs.
Generally, The 3D metal printing can be expensive compared to other 3D printing technologies. However, It is important to consider the total cost of the production process, which also includes the design of the 3D model, The preparation of the print file, the post-elaboration of the object and the maintenance of the 3D printer.